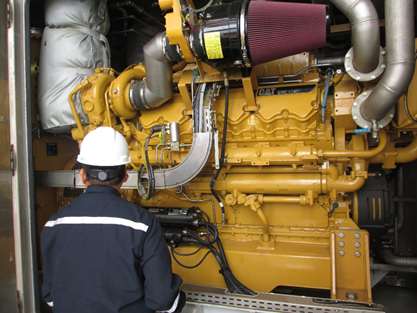
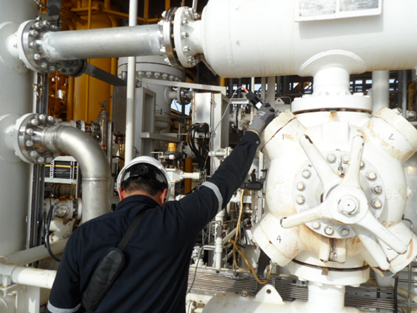
Introduction of Reciprocating Machinery Analysis
Reciprocating machinery analysis program is an application of combined analyses of critical operating parameters (pressure, temperature, vibration signal, and ultrasonic frequency) on reciprocating equipment for early detection of anomalies, reduction in efficiency, early stage of mechanical failure.
It needs to be performs on regular interval to establish baseline and operating trend. This program helps optimizing performance, preventing costly repair of the equipment, and minimize lost of production opportunity from equipment downtime.
How the technology works
Windrock Portable Analyzer consists of a set of Analyzers, transamitters, probes, sensors, encoders, and timing/strobe light to collect data. The information is analyzed by qualified engineer to generate trend analysis and determine abnormal condition.
Application and Problem detection of Reciprocating Machinery Analysis
Engine Analysis
Areas for assessing condition:
- Detonation
- Misfires
- Firing Pressure Imbalance
- Leaking Valves and Rings
- Worn or Scored Liners
- Primary and Secondary Ignition
- Performance Monitoring
- Turbo Charger Issues
Compressor Analysis
Areas for assessing condition:
- Leaking Valves, Ring and Packing
- Rider Band Wear
- Crosshead Wear
- Liner Damage
- Excessive Frame Vibration
- Lack of Rod Reversal
- Foundation or Grout Damage
- Looseness
- Performance Monitoring
Reciprocating Machinery Analysis
Areas for assessing condition:
- Misalignment
- Excessive vibration
- Looseness
- Defective bearing
- Foundation